Neil Wallace, MD of Aquaspira Limited on shaping the future of drainage systems for the Rail Industry – lower carbon, smarter products and fully integrated, digital designs
Ask anyone in the Rail Industry what represents digital innovation and next-generation technology, the last thing they will say is drainage. Nevertheless, as the 2021 Office for Road and Rail’s Annual Assessment of Network Rail pointed out, drainage systems are a critical part of the rail infrastructure. They are as important as track or earthworks when it comes to network resilience – so why not strive for more intelligent drainage systems? As the report highlights, improved monitoring of assets is desperately needed and the rail industry should “manage drainage as a critical asset and make the most of new technology”.
The challenge is to do this without impacting on the performance of the network it supports. Network Rail has reduced human trackside work by 45% and plan to phase it out completely. Clearly, better data and more autonomous monitoring will be required to make this happen. Drainage requirements are also evolving with severe, frequent weather events inevitably impacting on system performance and network safety. Upstream capture of storm water is vital for alleviating flash flooding and greater in-system holding capacity is needed to provide buffering at peak run-off periods. This requires integrated engineering and joined-up thinking at the design stage of drainage projects.
Network Rail recognises the challenges and in its “Improving Drainage Asset Management” and “Understanding Drainage System Capability” challenge statements, R&D actions are expected to develop new datasets, tools, models and decision-making systems in order to...
- Manage, view and map drainage
- Calculate the past, present and future demand on the system
- Account for factors such as degradation, capability analysis and flood risks
- Support the decision-making process and allow for timely intervention
Additionally, meeting Net Zero carbon by 2050 will be a challenge to the rail sector which traditionally relies on concrete as its material of choice. Not easy, so what can the drainage industry do to support Network Rail? Put simply, how can it innovate and provide the rail industry with the next generation of drainage systems to meet the challenges?
Promoting Pipeline Innovation
As a manufacturer of large-diameter, composite steel/plastic drainage pipes, Aquaspira understand how difficult meeting these challenges will be. Over the past few years, we have embarked on a programme of pipeline innovation (the “SmartSense” concept) that pulled in UK universities, key partners from the material supply chain and sensing experts to develop the next generation of pipeline systems. Core to SmartSense has been three themes of innovation - carbon reduction, digitally-enabled design and embedded sensing/monitoring; all pivotal for future drainage systems.
The Carbon Issue
It is a stark reality that UK construction accounts for 7% of GDP but also ~25% of greenhouse gas emissions. The pipeline industry is an integral part of the construction sector and needs to play a major role in the Net Zero journey. Developing low-carbon products is a must and, like many in the industry, Aquaspira have taken steps to reduce the embedded carbon of its pipes. Good carbon control starts in manufacturing and we have invested heavily in our material supply chain with new, low-carbon products using up to 80% recycled material without loss of product performance. Current research is focused on integrating mixed source materials and improving designs to optimise the use of recycled plastics.
The whole drainage system installation also has a carbon cost, which includes trench excavation and backfilling. Under current pipeline installation standards, fresh aggregate materials (usually sand and/or gravel) are required for the fill materials to guarantee pipeline integrity. As such, there is a significant added carbon footprint in the off-site removal of excavated soils and the import of virgin aggregates. It is estimated that the average transport distance from quarry to construction site is 40Km – a significant source of carbon emissions. Next generation drainage systems will have to utilise recycled ‘as-dug’ backfill materials to mitigate this carbon cost. This will reduce transport-related carbon footprints and facilitate the use of modern electric-based plant (diggers, etc.) rather than emission-heavy diesel vehicles.
Regulations are also a barrier with current standards for pipeline installation (e.g., BS 9295:2020 Guide to the Structural Design of Buried Pipes) not readily accommodating recycled materials in their scope. However, this standard is under review with carbon reduction an important element. The rail industry can take the lead here by being early adopters of the recycling approach and re-thinking how as-dug materials can be used in drainage system design.
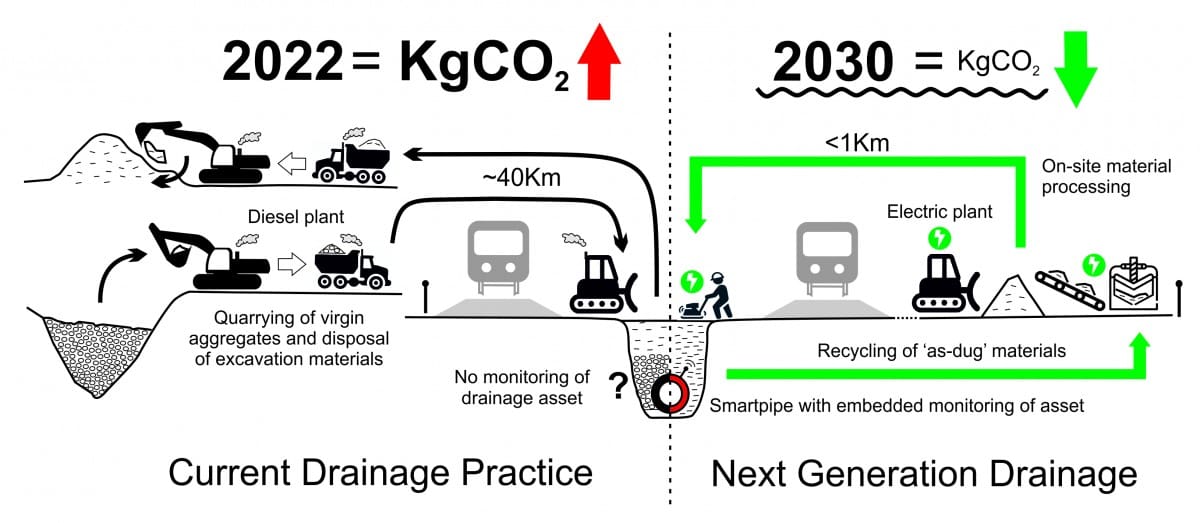
Carbon reduction through the next generation of drainage systems
Reaching net zero carbon by 2050 will require more integrated engineering where the whole drainage system is assimilated into the construction design process. This is where the second “SmartSense” concept applies with sophisticated numerical models being used to create digital simulants (Digital Twins) of pipeline installations that can link with BIM (building information modelling) software. Digital twin models allow for pipeline and installation properties to be included in a single model that can be digitally ‘tested’ under extreme performance conditions (e.g., heavy rainfall). The lack of models to inform new drainage system design has already been identified as a “priority problem” by Network Rail and digital twins, BIM-compatible product data and digitally-enabled designs will all play a part in the solution. At Aquaspira, we are developing digital twin models of our products that are tailored to rail network applications. These models will allow asset owners to evaluate and engineer drainage systems with greater confidence and embed future scenarios (e.g., climate change, system degradation, etc) into the modelling process.
This is a very powerful tool for network operators and an approach that should be considered for all future rail infrastructure projects.
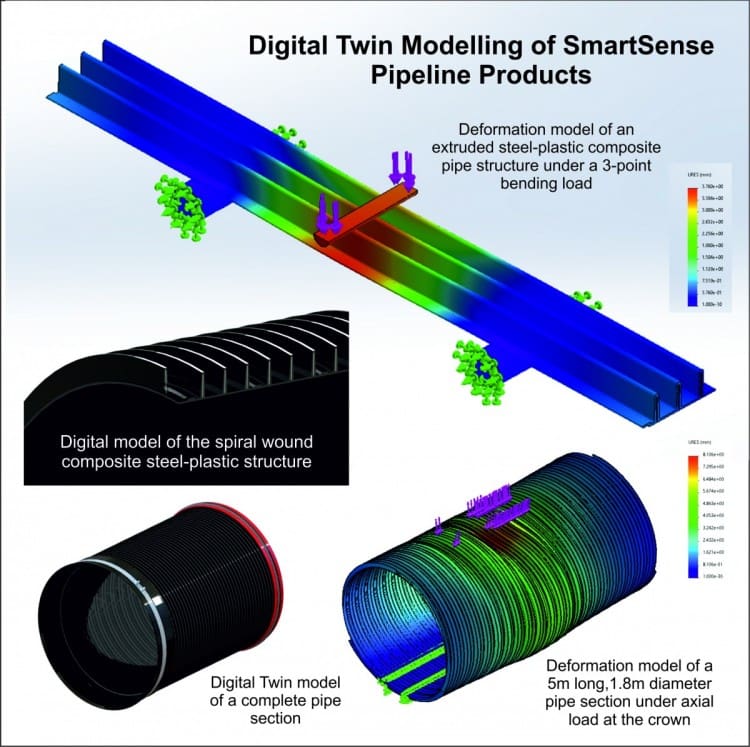
The Data Issue
Rail network owners lack reliable data to operate and maintain their infrastructure, be it trackside, at stations or in and around the network. Drainage systems are no exception and, arguably, represent some of the least monitored parts of the rail network. Collecting the right data, in the right place and at the right time is important for the next generation of drainage infrastructure. Having targeted, adaptable sensing capability is imperative and new pipeline products will have to monitor a range of conditions both in and around the pipes. This will become even more important as network maintenance regimes move away from ‘walking the track’ and towards autonomous monitoring.
Embedded sensing/monitoring is the third theme of the SmartSense concept where user-configurable sensing capability is integrated into the pipeline at the manufacturing stage. Sensing options can include strain, soil moisture & compaction, vibration and water flow/depth/temperature. More importantly, sensing configurations can be uniquely designed and tested through the Digital twin model so that monitoring-system performance can be evaluated at the pre-manufacture stage. Digital twins also provide the data-based requirements for compatibility with future maintenance and performance monitoring systems (i.e., virtual/augmented reality) plus accurate BIM-compatible data for construction sustainability and life-cycle assessments.
Ultimately, the sector is at the early stage of developing fully integrated drainage monitoring systems but as pipeline manufacturers, it is important that sensing capabilities match the needs of the rail industry. Demonstration trials recently conducted on the SmartSense product show that stress/strain sensing can not only monitor the performance of the pipe but also pick up changes in the surrounding soils due to ground movement and deformation. This has obvious potential benefits for the monitoring of earthworks but also critical, difficult to access structures such as bridges, tunnels and track components.
Making this smart pipeline concept work in real-world settings is the next step in SmartSense’s development and discussions with rail asset owners are already underway. It is up to pipeline manufacturers to innovate in digital design, sensing capability and carbon reduction to meet the needs of the rail industry. The positive news is that the process has already started - it is an exciting time to be part of a rapidly evolving sector that could make a real difference to the future of the rail network.
Tel: 01282 608510
Email: nw@aquaspira.com