New Civil Engineer article – Thames Water’s success with Aquaspira Composite Steel Reinforced Pipework in South East London
325m³
Required storage in sewer
93m
Length of pipe sections used
2.1m
Pipe diameters used
To read the full article by New Civil Engineer click here
Smaller external diameters and push-fit connections on composite steel reinforced pipework have saved Thames Water time and money on a sewer upgrade in south east London.
Residents of Dunoon Road in south east London have benefited from an upgraded sewer system with much less disruption during construction than normal. In the process of installing it, Thames Water also managed to reduce its costs and programme time.
In common with most urban flood alleviation schemes, the design team for Thames Water’s eight2O alliance faced the usual challenges of limited space in the road, existing utilities, and the need to create a solution that would minimise disruption for local residents and road users.
To provide the necessary storage capacity of 325m³ it was agreed that this could be achieved most efficiently by utilising a 93m long run of 2.1m diameter Aquaspira Composite Steel Reinforced (CSR) pipe.
Historically, attempting to fit conventional concrete pipes of this size into existing highways was extremely difficult, not only due to the much greater outside diameter of the pipes and the resulting wider and deeper excavation, but due to the practicalities of handling and installing pipes that weigh almost 10t. In stark contrast, the use of more modern composite materials enabled the trench width to be reduced by 500mm and the depth by 400mm, and weighing in at 400kg, the pipes could be handled with relatively small machines.
The smaller outside diameter of the pipes also enabled them to fit between, or beneath other existing utilities much better than conventional, more bulky pipes.
It was also recognised very early in the design process that access into the pipeline could not be achieved via large conventional manholes, which would simply not fit within the available space in the road. This challenge was overcome by incorporating Access End Pipes at each end of the pipeline, together with two Access Bends at intermediate locations along the run to accommodate minor changes in direction.
The prefabricated Access Units, supplied with the same sealed push-fit joints as the pipes, were also fitted with all necessary inlet and outlet pipe stubs to enable quick and simple connection to the adjoining pipe network.
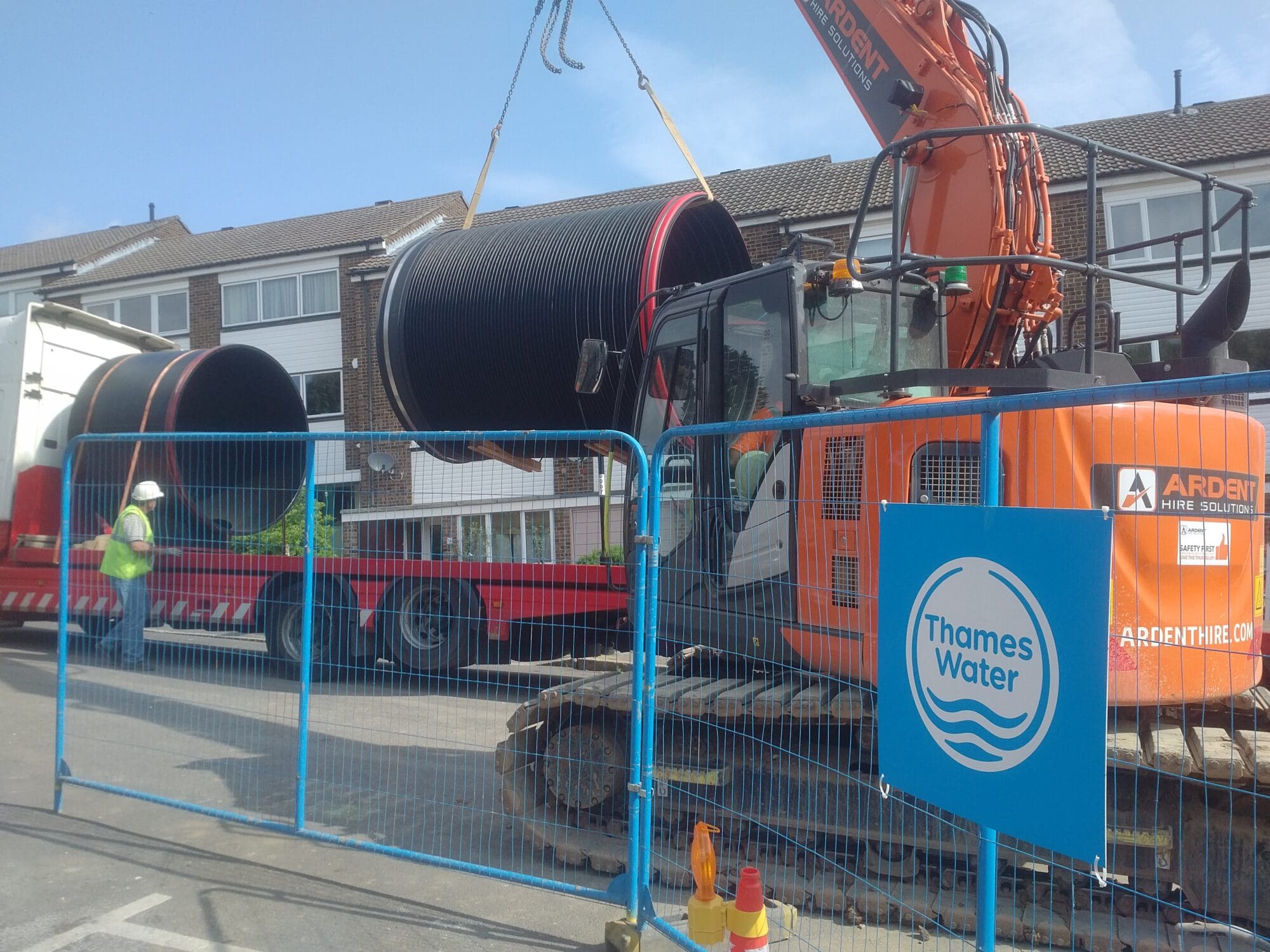
Thames Water senior general foreman, Andy Adaway, explains:
The technology from Aquaspira has seen a significant reduction in lorry movements on this project. It’s not only on deliveries where we have seen a reduction of more than 50% compared with a traditional concrete pipe installation, but equally important when working in London, ‘muck-away’ vehicles can be scarce, and when haulage is delayed, the work stops.
Much fewer muck-away trucks are required when installing Aquaspira pipes due to the trenches being shallower and narrower. On the Dunoon Road project, for example, muck-away tonnage was substantially reduced to 246t, compared to 354t with concrete pipe installations, and 465t with other plastic derived systems. This equates to a saving of up to 13 lorry movements to site, reducing costs, site management time, environmental impact and improving the safety of residents and workers, and of course, more than halving the HGV traffic emanating from the project.
Aquaspira’s unique push-fit joining system has also added to the success of the Thames Water project.
By simply lining up the spigot and socket joints on the two pipe sections and using the supplied jointing frame, the pipes push together and are sealed with a factory fitted integral rubber seal.
The bright red spigot gives a clear indication that the joint has been made, which proved to be very helpful for the installation team and site supervisors in terms of efficiency and confidence.
The very robust prefabricated access units are a massive improvement. Of course, they eliminate many of the problems and genuine safety issues associated with attempting to build huge manholes in roads with heavy concrete rings and slabs, but we’ve experienced difficulties on previous projects with large plastic chambers and pipes too.
More often than not, due to either rain or groundwater, in deep excavations we’re working in wet conditions. The method of jointing large plastic pipes and chambers that have been installed in the past has involved insitu welding, which in wet conditions is inherently difficult and, by definition, requires risk assessment and method statements to manage the safety of men working and undertaking hot welding operations in confined spaces below ground for long periods of time.
The Thames Water eight2O alliance takes its responsibility to reduce carbon and the overall environmental impact of all projects very seriously, and this was no exception. The ability to reduce transport to and from site by over 50%, together with a 25% reduction in excavation, contributed towards a significant decrease in emissions from vehicles and plant. In addition to operational benefits, pipes manufactured from composite steel reinforced polyethylene in this diameter utilise 30% less material than alternative plastic pipes and contain over 25% recycled material.
Following the success of the project at Dunoon Road, Thames Water’s eight2O alliance partnership is already incorporating the AquaSpira pipe and access system into designs for future schemes.
Approval is also in place for developers to use the system on adoptable drainage systems, where the same significant savings in cost, programme time and disruption can be achieved, in addition to the major improvements to safety and carbon reduction.
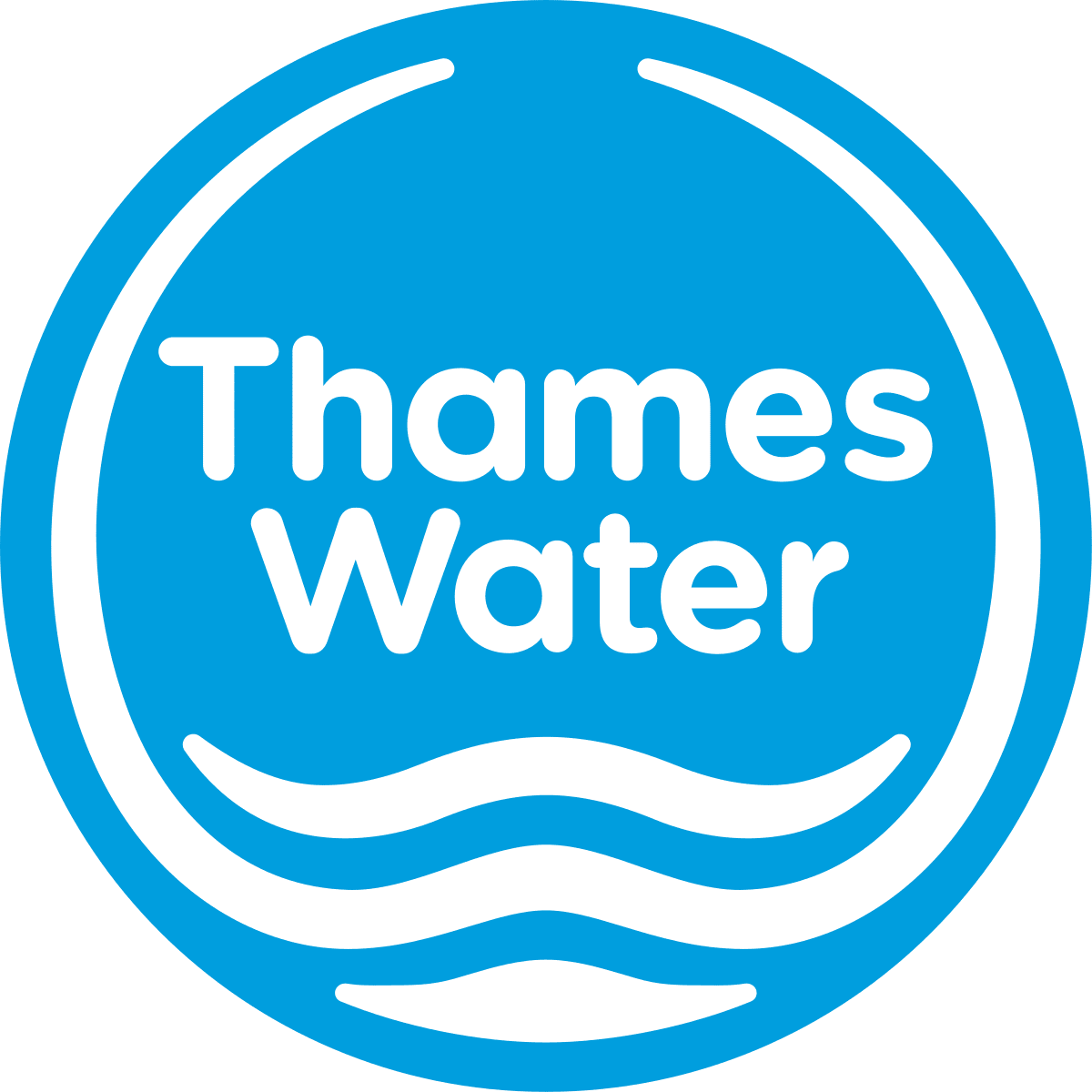
Working with the Aquaspira system is completely different. The access units are much sturdier and can be firmly fixed into position and, rather than being a major concern, the push-fit joints with integral ring-seals enabled us to connect pipes together in a matter of seconds, fully sealed – fit and forget!
Andy Adaway
Senior General Foreman | Thames Water